Ecommerce Fulfillment
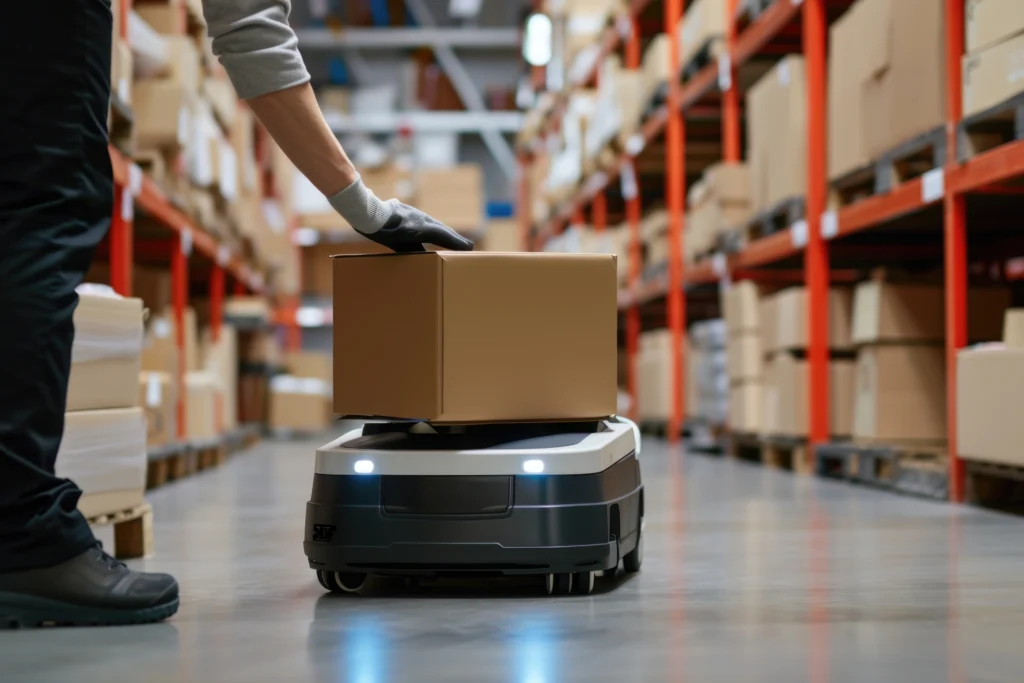
Ecommerce Fulfillment Provider in Bhiwandi -
In the fast-paced world of e-commerce and logistics, speed and accuracy can make or break your reputation. One of the most critical—and often overlooked—elements of a successful fulfillment process is the Pick, Pack, and Ship workflow. No one wants to wait months for their package to arrive, and you want to ship as many products as possible to maximize profits. Both you and your customers benefit from an efficient, streamlined order fulfillment process. Here’s how you can make your shipping operations leaner and smarter.
Robin Enterprises : Trusted Ecommerce Fulfillment Provider help to organize the process of the operation includes a variety of services for businesses that want to outsource their order fulfillment needs.
Tips to Optimize Your Pick, Pack, and Ship Process -
Ecommerce fulfillment Provider helps to organised your Pick, Pack, and Ship Process.
1. Pick
Once a customer orders an item from your store, your fulfillment provider managing inventory and order processing. This process is tougher when you’re working with a large inventory. So, many ecommerce fulfillment provider use a warehouse management software (WMS) tool to help them find items fast. Here are some following picking strategies –
- Piece Picking : Piece picking is the most common and straightforward method. It’s when your picker travels to the item’s location, pulls it off the shelf, and carries it out. Similar to how you might find something at the grocery store. This works for small orders, but it can be inefficient for larger batches.
Batch Picking : Batch picking reduces the amount of time your picker spends locating items. Batch pickers collect items for multiple orders at the same time. It’s a good choice for items located near the back of your warehouse. Batch pickers typically use hand carts or pallets to carry items.
Wave Picking : Also known as cluster picking, wave picking occurs when pickers are scheduled to collect orders in intervals. These intervals are your “waves.” Typically, pickers collect items for 3-12 orders per interval. It’s good for suppliers that get several high volume orders per day.
Zone Picking : Zone picking is also referred to as the “pick and pass” method. It’s when you divide your warehouse into specific zones and assign pickers to each zone. You can train your pickers to become specialists in their assigned zone. This helps reduce time spent locating items.
2. Pack
After locating everything on your picking list, you must pack these items before shipping. Often, employees at your warehouse pick and pack the items for you. So, remember to provide them with sufficient packing materials too.
Both processes can occur at the warehouse, but pickers and packers aren’t usually the same people. Once the picker locates the items, they forward them to the packing station. Like picking strategies, it’s important to choose the right packaging for each order, from corrugated boxes to plastic boxes.
You should also include a packing slip with each order. Packing slips help packers understand what needs to be packed, and customers use them to check that what they ordered is there. Packing slips must include:
- Customer address and contact info: Your shipping label will include this information, but you should also include it on your packing slip as backup.
- List of items and the quantity of each item: Customers like cross-referencing their orders with your slips.
- Any out-of-stock items that were ordered but not fulfilled: Always notify the customer ahead of time in this situation. However, it’s a good practice to have it in writing on the packing slip too.
- Each item’s SKU or UPC number: This is what you use to track inventory and reference the specific item if there are any issues.
- Slip or PO number: This helps you and your customer verify that the right order went to the right person.
3. Ship
At this point, it may be tempting to think the work is over. The biggest thing you must remember is to calculate the cost of shipping before you send out your package.
Calculating in advance prevents you and the customer from seeing any surprise charges. For example, some countries have duty fees that you need to plan around. Other factors that increase shipping costs are:
- Weight
- Dimensional size
- Priority shipping
- Value of content
- Shipping zone
Each step may seem simple on its own, but when scaled across hundreds or thousands of orders daily, the process becomes increasingly complex. That’s why outsourcing to a fulfillment provider can make all the difference.
Why Streamlining Matters -
Faster Order Fulfillment
A well-optimized system allows staff to fulfill orders more quickly. With automation tools, barcode scanners, and smart inventory management systems, you can cut down the time from order to delivery dramatically.
Reduced Human Error
Manual processes are error-prone. An integrated system that manages picking lists, verifies item codes, and tracks inventory in real-time can reduce mistakes and improve accuracy.
Cost Efficiency
Inefficiencies add up. Streamlining reduces wasted materials, labor costs, and shipping errors—all of which can hit your bottom line.
Improved Customer Satisfaction
Late shipments or incorrect orders are major contributors to poor reviews. A faster, more accurate fulfillment process ensures customers receive exactly what they ordered, and on time.
How a Fulfillment Provider Streamlines the Process -
Advanced Technology & Automation
As an experienced ecommerce fulfillment provider, we use robust warehouse management systems (WMS) that automate everything from pick lists to label printing. This not only increases speed but drastically reduces errors.
Optimized Warehouse Operations
Our fulfillment centers are strategically organized to minimize travel time and maximize efficiency. High-volume SKUs are easily accessible, and real-time inventory syncing ensures that stockouts and oversells are avoided.
Custom Packing Solutions
We know that packaging is more than just protection—it’s part of your brand experience. We provide custom kitting, eco-friendly packaging options, and standardized packing procedures that reflect your brand values.
Fast, Reliable Shipping
With carrier integrations and negotiated shipping rates, we get your orders out the door quickly and affordably. Plus, real-time tracking updates keep your customers informed every step of the way.
Ready to Streamline Your Fulfillment?
If your business is growing and your shipping process is starting to feel like a bottleneck, it might be time to level up. Partnering with Robin Enterprises your trusted fulfillment provider can simplify operations, reduce costs, and deliver a consistently excellent experience to your customers.
Let us take care of the Pick, Pack, and Ship—so you can focus on what you do best: building your brand.
Your Trusted Warehousing Partner !
Related Posts
Best Ecommerce Fulfillment Services : A Key to Online Business Success
Ecommerce Fulfillment March 15, 2025 Robin Enterprises E-commerce Fulfillment Services and Warehousing Service in Bhiwandi – Robin Enterprises : Trusted Partner for All Your Ecommerce…